Hazardous Area Management
Hazardous Area Management
OCS is the global leader in the supply of management services for Hazardous Area Equipment and management. There are few companies that can supply full support for your inspections and maintenance as OCS with the full suite of services listed below;
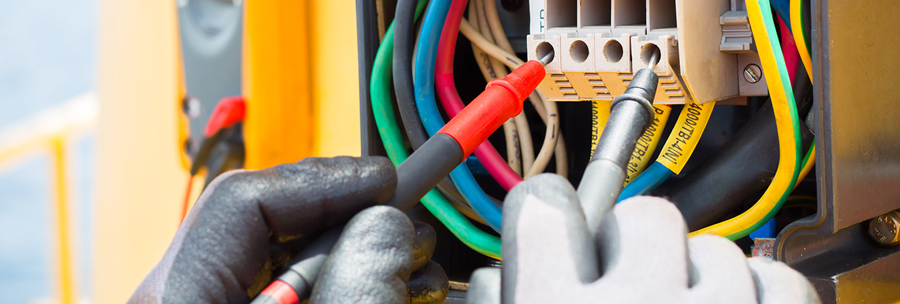
Installation, Commissioning and Dossier Generation: During the installation & commissioning phase of an asset the hazardous area equipment needs to be installed, inspected and documented correctly to ensure compliance. This initial inspection is critical to ensure that all equipment is correctly installed so that a good baseline has been established this then can be used as a starting point to form the basis of a maintenance strategy that will best suit your asset and maintenance requirements. OCS Group is a leader in developing and providing this service and if completed correctly and by using the PDA software will make the maintenance process much more efficient with exceptional cost savings can be realized over the asset life cycle, this can be demonstrated by making a business. Inspections: OCS Group is the industry leader in providing global hazardous area inspections, with clients consistently requesting repeat services. Our technician and inspectors have many years of experien
Hazardous Area Equipment Strategy Most companies take a periodical approach to their Hazardous Area Equipment Inspection Management which inspects all equipment over a certain period of time; this may be 3 years or 5 years. Some companies may do visual inspections while others may select to do a percentage of detailed inspections and others a combination of visual and detailed inspections each year until all equipment has been inspected over the cycle period. This process is then repeated. Variations of this process may vary pending local Statutory Requirements. An alternative approach would be to develop a Risk Based Inspection Strategy. This looks at the management of the equipment in a different manner than in a periodical approach which may be more effective for your operation, especially where large numbers of equipment are involved. This strategy takes into condition of ignition risk criteria and forms the basis of a Risk
The advantages of this approach is that it significantly reduces the number of pieces of equipment needed to be inspected by only inspecting a proportion of the total equipment. When adopting a risk based approach a thorough review of the equipment is required such as, location/environment, protection methods and ignition risk including various factors are taken into consideration. This information together with a solid base of historical collated inspection information and fault records is required to form the basis of a Risk Base Strategy. Using this data, a sample inspection process can be determined that would be dependent on the risk factors mentioned above which governs a percentage of inspections to be conducted for various lots. The success of this process requires measured and accurate KPIs that will justify your approach; these are reviewed annually to ensure that the integrity of the equipment has not been reduced past a predetermined level known as the As Low as R